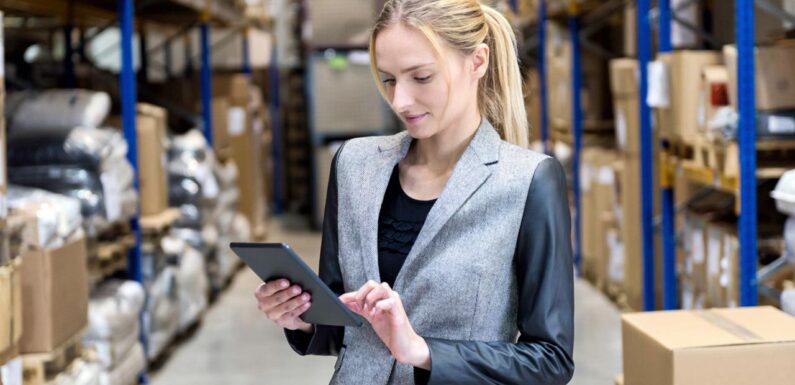
Controlling inventory in a manufacturing business can be a difficult task that many companies don’t know how to handle.
Multiple factors impact the inventory count, which needs to be managed. The absence of a proper system in place can result in decreased efficiency and increased waste and loss.
Inventory management software can track produced items, incoming supplies, sold products, damaged goods, and shipped items. The collected information can help businesses make better production decisions to avoid under or overproductions leading to stock inaccuracies.
Businesses that don’t use inventory control systems might suffer from the inability to keep track of their products. Manufacturing companies who aim to become more productive should find and integrate the best kind of management systems.
Inventory management system
Depending on the exact control techniques that are used by manufacturers, inventory management systems can take multiple forms. However, all of them can be extremely beneficial to manufacturers by keeping track of goods and supplies produced as the software monitors incoming supplies, stores items, shipped goods, and produced products.
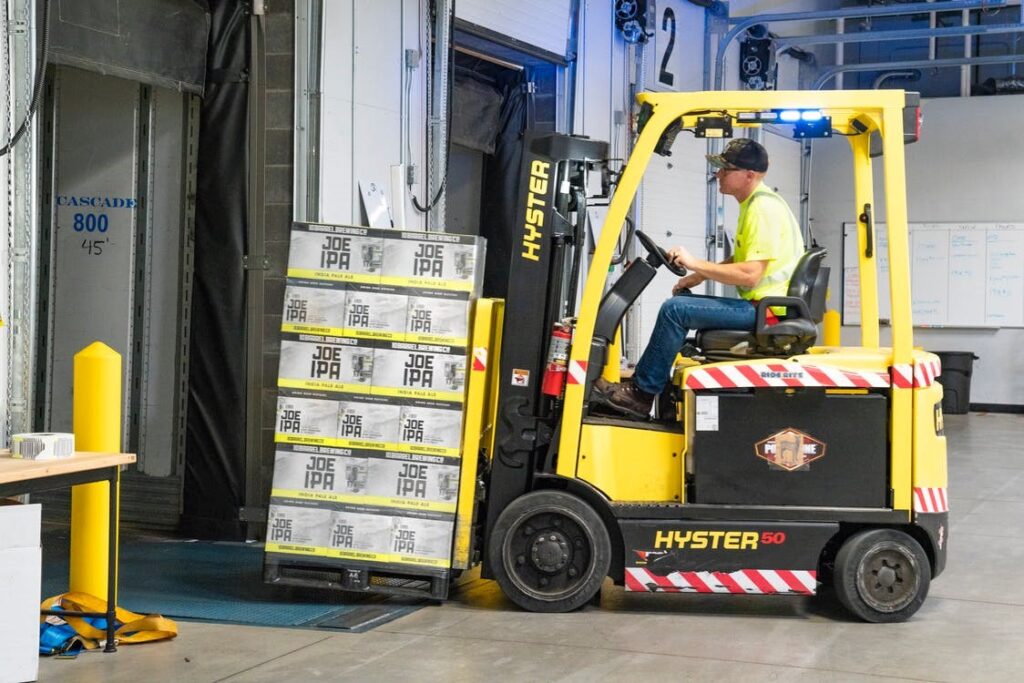
Inventory control techniques
Inventory management systems can easily adapt to many control techniques:
Just-in-time
JIT management is extremely rewarding even though it carries many risks. Manufacturers can only stock supplies that they’ll need immediately. Storage space is reduced by getting parts within hours of their expected use. However, unexpected delays like a natural disaster, spikes in demand, or delivery issues can be problematic and can ruin the fragile balance of this control technique.
ABC analysis
The basis of ABC analysis comprises calculating the sales potential of items and assigning them accordingly. Items with the highest value are assigned as A, equating to 20% of the total. Middle-value items with lower selling demand make up 30% of the inventory while the rest falls into C, with the lowest value.
Economic order quantity
EOQ aims to find the perfect balance between sales and supply orders to minimize extra order and stock occurrences. It uses both the holding and setup costs of the inventory to calculate the total cost.
Set-the-levels
The first step in set-the-levels management is to establish maximum and minimum values for tock items. The business orders more once the values fall below the minimum requirement, and production or purchasing pauses if they reach the maximum.
First-in, first-out
FIFO is the best inventory management system for perishable goods since it sends out the oldest items first to prevent them from spoiling or expiring in the storage. Food manufacturers usually use this method for selling food before its labeled expiration date.
Benefits of using inventory management systems
Manufacturers can enjoy a variety of benefits from integrating an inventory management system:
1. Save money
Goods waiting to get shipped can take up a large chunk of expenses as they sit in a warehouse. It can become cost-prohibitive to have a large warehouse depending on the real estate prices of the location. A proper inventory management system can help keep the number of products that need storage low, reducing the overall storage space required.
2. Decreased risk of going out-of-stock
Effective inventory systems keep up with the current number of stock that’s available by making use of perpetual counting. Customers will be spared from shipping delays and dissatisfaction from buying out-of-stock items when a business knows what it has on hand.
3. Simplify management
Inventory management systems make tracking orders, stored products, and production much easier. Managers can focus on the business operations instead of customer complaints with the help of this system.
4. Forecast your future sales accurately
Information that’s obtained from inventory management systems can give insight into previous sales trends. Manufacturers can make better, informed decisions about production amounts based on this data. This can enable them to avoid over or underproducing.
Get one of the best inventory management software for the manufacturing industry
Make your sales tracking more efficient with the help of POS software for furniture retailers, barcode inventory management software, and barcode inventory systems for restaurants, home furnishing stores, wholesale businesses.